PET film printers have revolutionized the printing industry by enabling high-quality and efficient printing on various applications. However, understanding the factors that influence the printing speed of PET film printers is crucial for optimizing productivity and meeting production deadlines. In this article, we will explore the key factors that impact the printing speed of PET film printers and discuss strategies to enhance efficiency.
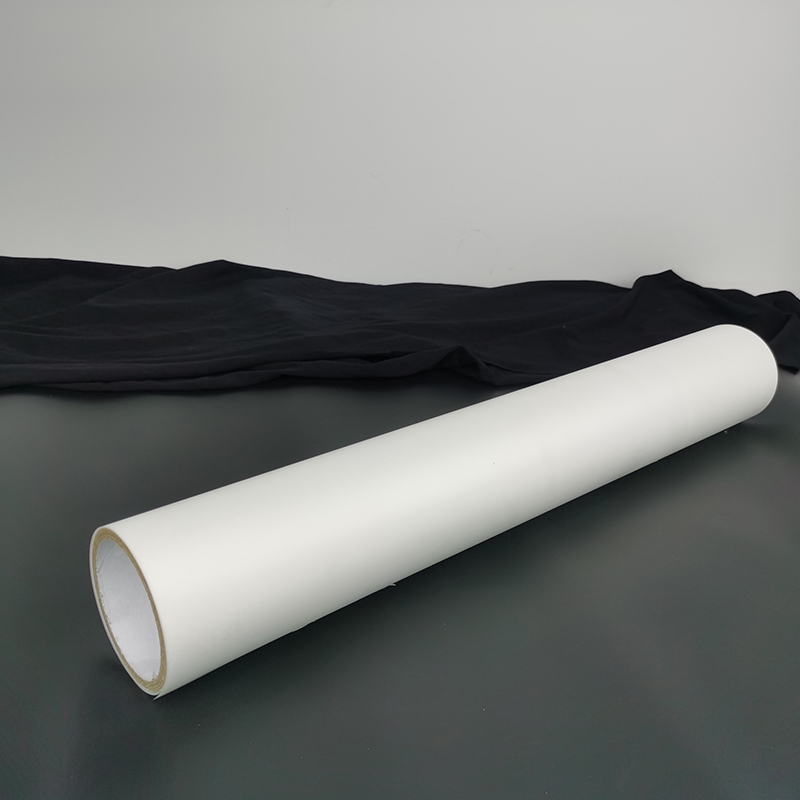
Print Resolution: One of the primary factors affecting printing speed is the chosen print resolution. Higher print resolutions require more ink droplets and finer details, resulting in a slower printing process. To increase printing speed, consider using a lower print resolution when appropriate, especially for applications where fine details are not crucial. Balancing print resolution and desired output quality can help optimize printing speed without compromising overall print results.
Image Complexity: The complexity of the image or design being printed directly influences the printing speed. Intricate designs with a high level of detail, gradients, or multiple colors require more time to process and print. Simplifying designs or optimizing them for faster printing can significantly improve printing speed. Consider optimizing images by reducing unnecessary details, minimizing gradients, or converting images to more printer-friendly formats to expedite the printing process.
Printer Technology and Configuration: The type of printer technology used for PET film printing, such as inkjet or digital printing, can impact printing speed. Different printer models offer varying speeds and capabilities. Ensure that you choose a printer model optimized for speed if fast printing is a priority. Additionally, configuring the printer settings, such as print mode (draft, normal, or high quality) and speed settings, can further influence the printing speed. Experiment with different configurations to find the optimal balance between speed and print quality.
Drying and Curing Time: PET film printing typically involves the use of specialized inks that require drying and curing after printing to ensure durability and longevity. The time needed for ink drying and curing can affect overall printing speed. Utilizing fast-drying and quick-curing inks specifically designed for PET film printing can help minimize drying and curing time, allowing for faster print production.
Printer Maintenance and Performance: Regular maintenance of the PET film printer is essential for optimal performance and printing speed. Neglected or poorly maintained printers may experience mechanical issues or decreased efficiency, leading to slower printing speeds. Follow the manufacturer's recommended maintenance schedule, including cleaning, lubrication, and inspection of printer components, to ensure smooth operation and maximum speed.
Workflow Optimization: Efficient workflow management can significantly impact the overall printing speed. Analyze the entire printing process, from file preparation to printing and finishing, to identify any bottlenecks or inefficiencies. Streamline the workflow by automating repetitive tasks, utilizing pre-press software for faster file processing, and implementing efficient job scheduling. Minimizing downtime between print jobs and optimizing the sequence of printing tasks can further enhance printing speed.
Hardware and Connectivity: The hardware components and connectivity options of the PET film printer can influence printing speed. Ensure that the printer is equipped with adequate processing power, memory, and data transfer capabilities to handle high-speed printing. Additionally, optimizing connectivity, such as using high-speed USB or Ethernet connections, can help eliminate data transfer bottlenecks and maintain consistent printing speeds.
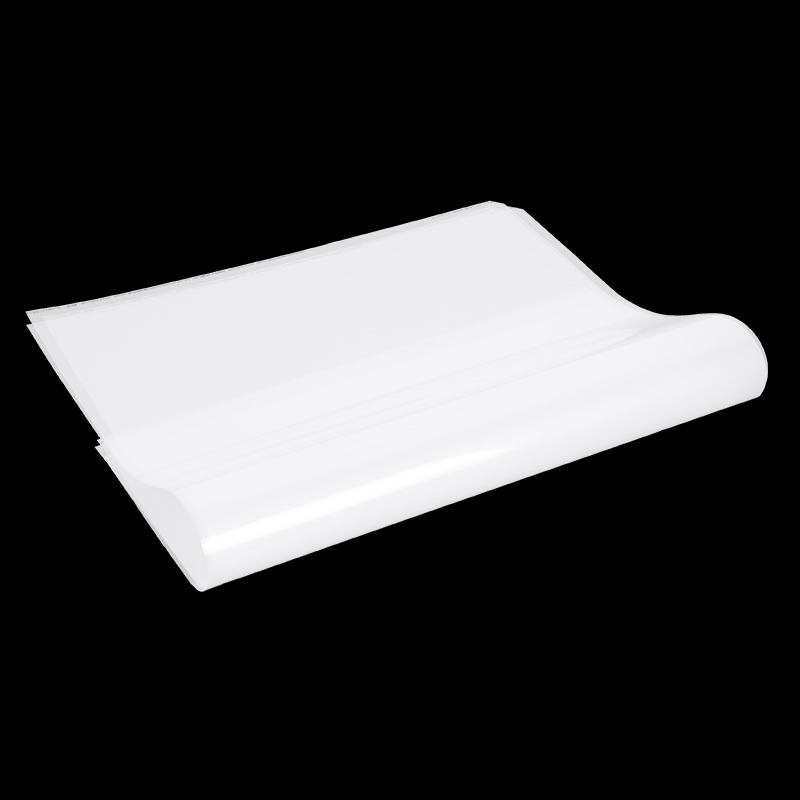
The printing speed of PET film printers is influenced by various factors, including print resolution, image complexity, printer technology and configuration, drying and curing time, printer maintenance and performance, workflow optimization, and hardware and connectivity. By understanding these factors and implementing appropriate strategies, such as adjusting print settings, optimizing image designs, selecting the right printer model, using efficient inks, and streamlining workflow processes, PET film printer owners can enhance printing speed and productivity. Remember to strike a balance between speed and print