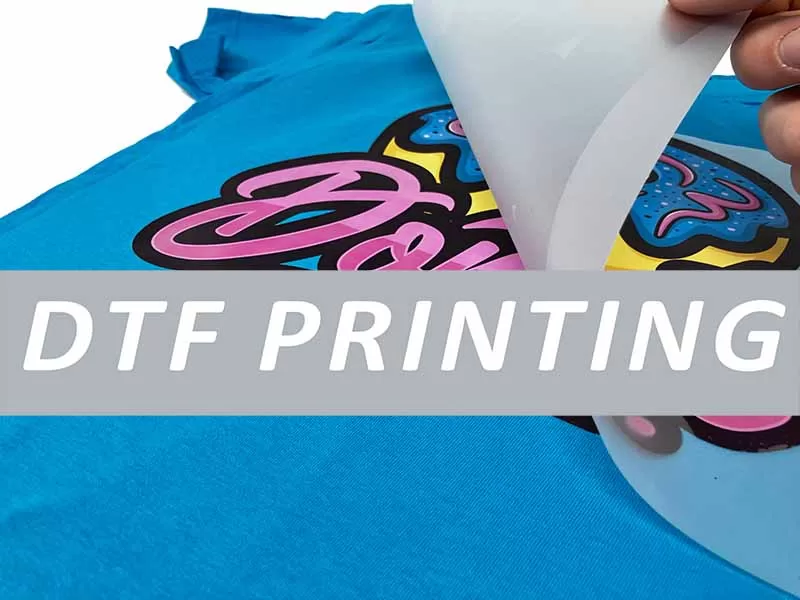
Q1: What is the difference between DTF and UV DTF?
A: DTF (Direct-to-Film) printing involves transferring designs directly onto a specialized PET film, which is then applied to the substrate using heat and pressure. UV DTF refers to the same process but utilizes UV-curable inks instead of traditional pigment or dye sublimation inks. UV DTF offers faster curing times and can be suitable for specific applications that require immediate curing or compatibility with UV printing systems.
Q2: Which printers are available for DTF printing?
A: DTF printing is compatible with a variety of printers, including Epson SureColor models, Epson EcoTank printers, and other compatible inkjet printers. It is important to check the printer's compatibility with DTF inks and the necessary firmware or software updates for optimal performance.
Q3: Do you need special software for DTF printing?
A: Yes, specialized RIP (Raster Image Processor) software is often required for DTF printing. This software helps manage color profiles, ink density, and allows for seamless integration between the printer and the DTF process. It ensures accurate image reproduction and enhances overall print quality.
Q4: How is the wash resistance of DTF prints?
A: DTF prints generally offer good wash resistance when properly applied and cured. The wash resistance can vary depending on factors such as ink quality, substrate type, curing process, and post-processing techniques. It is advisable to follow specific manufacturer recommendations for optimal wash durability.
Q5: Why does the printed DTF PET film turn oily after drying for a while?
A: The oily appearance on the printed DTF PET film is caused by excess adhesive powder that was not fully activated during the curing process. This excess powder can migrate to the surface of the film, resulting in the oily appearance. Proper curing time and temperature, as recommended by the manufacturer, can help minimize this issue.
Q6: What is the solution to the DTF transfer smudge problem?
A: DTF transfer smudging can occur if the ink is not sufficiently cured or if the proper pressure and temperature are not applied during the transfer process. To avoid smudging, ensure that the ink is fully cured, use adequate pressure during transfer, and follow recommended curing guidelines provided by the DTF manufacturer.
Q7: Can I print on DTF film with DTG ink?
A: No, DTG (Direct-to-Garment) inks are specifically formulated for printing directly onto fabrics and are not suitable for DTF printing. DTF printing requires specialized DTF inks that are designed to adhere to the PET film and provide the necessary durability and color vibrancy.
Q8: Are DTF prints suitable for all types of fabrics?
A: DTF prints are generally compatible with a wide range of fabrics, including cotton, polyester, blends, and even some synthetic materials. However, the specific compatibility may vary depending on the quality of the fabric and its reaction to heat and pressure. It is recommended to test DTF prints on a small sample of the fabric before full-scale production.
Q9: How does DTF printing compare to other printing methods like screen printing or sublimation?
A: DTF printing offers advantages such as the ability to print intricate designs with vibrant colors, compatibility with various fabrics, and relatively easy setup. It also provides flexibility in terms of print size and the potential for high-resolution printing. However, DTF printing may require additional post-processing steps compared to screen printing or sublimation. The choice of printing method depends on specific requirements, volume, and desired outcomes.
Q10: Can DTF prints be used for outdoor applications?
A: DTF prints are primarily intended for indoor applications. While they can withstand normal wear and tear, they may not have the same level of durability and resistance to outdoor elements as other printing methods like screen printing or UV printing. If outdoor use is necessary, additional protection such as laminating or coating may be required to enhance durability and longevity.
Q11: How does the cost of DTF printing compare to other printing methods?
A: The cost of DTF printing can vary depending on factors such as ink consumption, film quality, and printer maintenance. Generally, DTF printing can offer a cost-effective solution for small to medium-scale production runs compared to methods like screen printing, especially when it comes to multi-color designs or intricate patterns. However, for large-scale production, other methods like screen printing or sublimation may be more cost-effective.
Q12: Are there any environmental considerations with DTF printing?
A: DTF printing involves the use of PET film and adhesive powder, which may raise concerns about environmental impact. However, some manufacturers offer eco-friendly versions of DTF products that minimize waste and reduce environmental footprint. It is recommended to choose suppliers that prioritize sustainable practices and offer eco-friendly alternatives.
Q13: Can DTF prints be applied to dark-colored fabrics?
A: DTF printing is suitable for both light-colored and dark-colored fabrics. For dark fabrics, an additional layer of white ink is typically printed as a base layer before applying the colored inks. This ensures vibrant and accurate color reproduction on dark backgrounds.
Q14: How long do DTF prints last?
A: The longevity of DTF prints can vary depending on several factors, including ink quality, fabric type, laundering methods, and proper curing. With proper application and care, DTF prints can maintain their color vibrancy and durability for an extended period. However, it is important to note that over time, exposure to sunlight and repeated washings can gradually impact the appearance and longevity of any printed material.
Q15: Can I use DTF printing for promotional products or personalized items?
A: Yes, DTF printing is well-suited for creating custom promotional products and personalized items. Its versatility allows for printing on various substrates, such as t-shirts, bags, mugs, and more. The ability to produce vibrant, full-color designs with intricate details makes DTF printing a popular choice for customized merchandise.
Remember to consult manufacturers' guidelines, perform proper testing, and seek professional advice to ensure optimal results and to address any specific concerns regarding DTF printing.